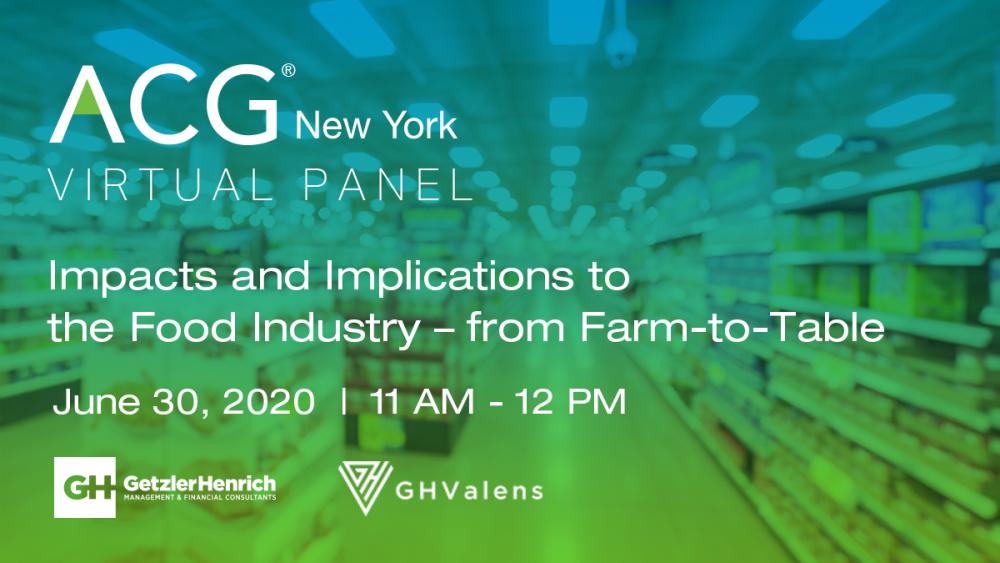
Overview
The pandemic is causing both temporary and permanent changes to every component of the food value chain from both demand and supply perspectives. The initial impacts are positive in some sub-sectors, while disastrous in others. What is common across all sub-sectors is the need to adapt and ultimately stabilize businesses for long-term sustainability and less vulnerability to shocks.
High level impacts registered thus far:
- Sales of food staples (e.g., pasta, sauces, breads, etc.) are significantly higher
- Specialty and prepared foods sales are significantly lower
- Customer demand is unexpected in some areas, but generally causing stress within organizations and supply chains
- Health safety procedures causing productivity declines and increased overhead costs (i.e., use of PPE, mandatory social distancing in manufacturing and aggregation environments, and temperature checks)
- Availability of both trained and untrained labor causing productivity declines, reductions in output, increased focus on personnel and human resources matters.
More specific challenges and opportunities seen by each segment of the farm-to-table value chain include:
- Agriculture
- Challenges: Supply chain bottlenecks, particularly with imported sources of supply, travel restrictions limit, ability to attain supply contracts, working capital, customer plant closures
- Opportunities: Still operating as “essential”, improved forecasting, farm to food bank efforts
- Processing and Packaging
- Challenges: Supply chain bottlenecks, customer demand, social distancing requirements within plants, increasing employee absenteeism and health concerns, inefficiency in maintenance and repair operations, limited sources of supply for approved packaging
- Opportunities: Employ Lean approaches to maximize output with fewer and more distanced labor, price increases to cover higher costs, repurposing packaging, recycling
- Distribution and Aggregation
- Challenges: Shifts in origin-destination routes due to diminished restaurant demand, limitations to delivery due to customer drop-off restrictions, availability of drivers, sanitization costs
- Opportunities: Changing routes and optimizing the entire logistics network, rethinking hub-spoke models for distribution centers/warehouses and stores/customers, changes to packaging to maximize container and shelf space
- Retail - Grocery
- Challenges: Surging customer demand in specific product categories; ability to meet stocking needs, customer service – including health and safety, increasing cost impact to already low margins (from labor, sanitization costs, altered hours and services, etc.)
- Opportunities: SKU prioritization, pricing optimization, re-thinking shelf-space, reduce shrinkage, increase market share, delivery
- Retail - Restaurant
- Challenges: Slow and limited re-openings, supply chain bottlenecks, restrictions on customer capacity, higher costs associated with cleanliness, hygiene, food safety, availability of labor
- Opportunities: Consolidation of food prep and delivery operations, re-thinking dining space, take-out / pick-up service, delivery
Speakers
Sponsors
Event Materials
Please contact Amanda Luckie at aluckie@acgnyc.org for questions or more information.